Materiały płuczkowe – klucz do efektywnego wiercenia
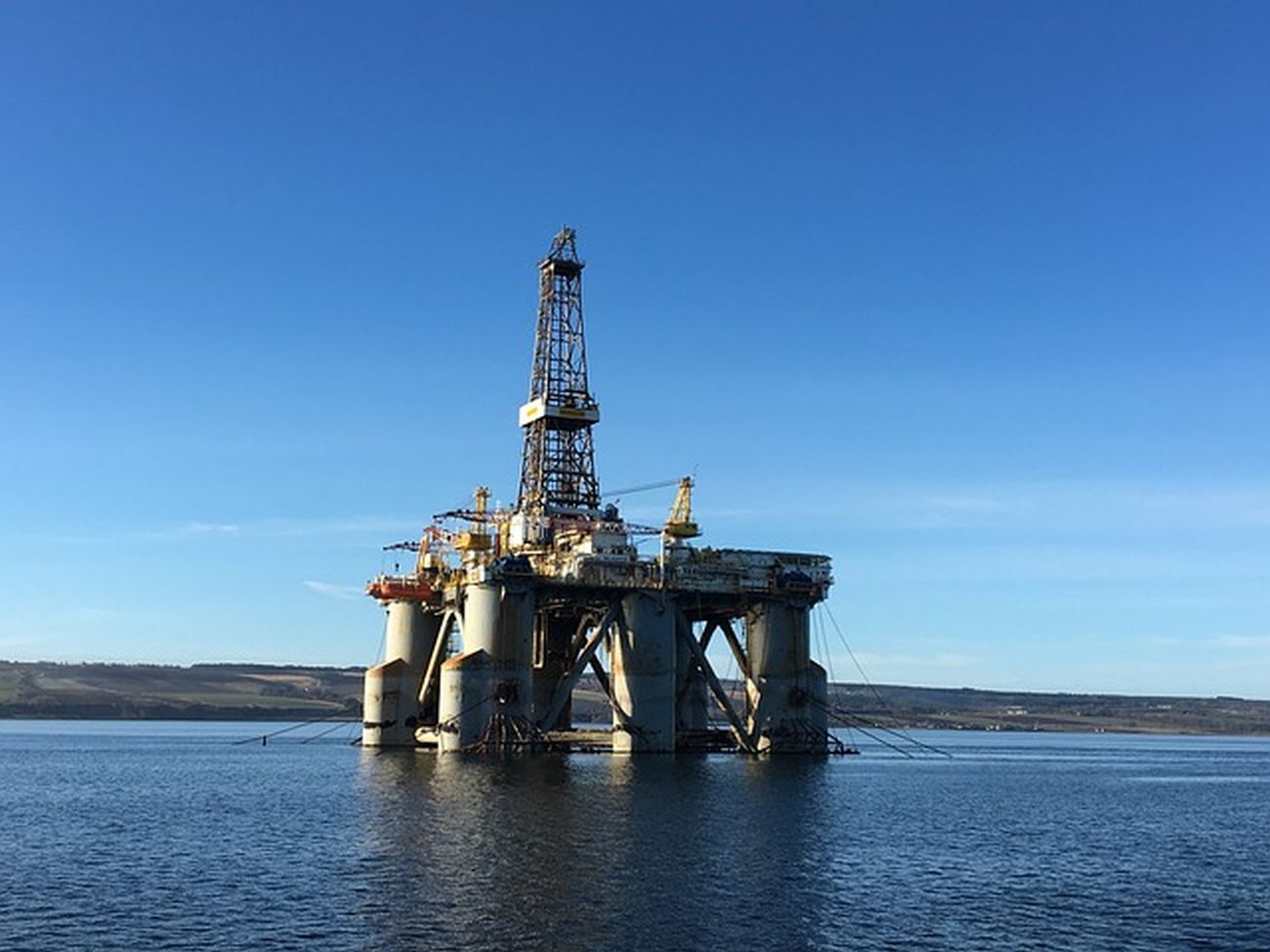
Zastanawiasz się, jakie materiały płuczkowe zapewnią największą wydajność procesu wiercenia? Poznaj kluczowe informacje o polimerach, bentonitach oraz innych składnikach, które wpływają na szybkość, koszty oraz trwałość wiercenia.
Najważniejsze informacje
- Materiały płuczkowe są istotne dla efektywności wiercenia; zapewniają chłodzenie, smarowanie narzędzi wiertniczych, stabilność otworu wiertniczego, a także redukcję kosztów i czasu.
- Wybór materiałów płuczkowych jest procesem zindywidualizowanym i zależy od specyfikacji projektu – wymaga analizy warunków geologicznych i technologicznych w szczególności odporności, właściwości chemicznych oraz kompatybilności z innymi elementami wiertni.
- Optymalizacja procesu wiercenia dzięki materiałom płuczkowym obejmuje poprawę stabilności ścian otworu, redukcję zużycia narzędzi wiertniczych i minimalizację strat płuczek, a także dbałość o bezpieczeństwo i wpływ na środowisko, w tym biodegradację i zarządzanie odpadami wiertniczymi.
Zastosowanie materiałów płuczkowych w wierceń
Materiały płuczkowe są kluczowe dla efektywnego wiercenia. Do powszechnie stosowanych materiałów płuczkowych w kierunkowych wierceniach horyzontalnych zaliczają się polimery, bentonity oraz inne materiały. Pełnią one istotne funkcje, takie jak chłodzenie i smarowanie narzędzi wiertniczych, co jest kluczowe dla zapobiegania przegrzewaniu się i przedwczesnemu zużyciu, a także pozytywnie wpływają na czas wiercenia, co przekłada się na oszczędności kosztów.
Cechy idealnego materiału płuczkowego dla procesu wiercenia obejmują:
- zapewnienie stabilności otworu wiertniczego zarówno w pionie, jak i w poziomie
- stanowienie fundamentu sprawnego prowadzenia robót wiertniczych
- utrzymanie odpowiednich właściwości umożliwiających wydajne wiercenie
Materiały płuczkowe, takie jak osad z płuczki wiertniczej, mają potencjał znacznego poprawienia efektywności wiercenia.
Dodatkowo, zastosowanie płuczki pianowej może zwiększyć prędkość wiercenia otworów o większych średnicach, co z kolei przekłada się na wzrost wydajności pracy.
Polimery
Polimery organiczne są najczęściej wykorzystywanymi materiałami płuczkowymi, ponieważ mogą być dodane do zawiesiny bentonitowej w celu modyfikacji jej właściwości reologicznych. W pierwszej fazie wiercenia polimery stabilizują ściany odwiertu, a po zapuszczeniu rur mają przewagę nad bentonitem, zwłaszcza pod względem tych aspektów.
Bentonity są najbardziej optymalne jako materiały płuczkowe, gdy są wykorzystywane jako źródło węgla organicznego oraz gdy stymulują specyficzne dla polimerów procesy pełzania i relaksacji naprężeń, co jest korzystne w określonych warunkach geologicznych i technologicznych.
Bentonity
Bentonit jest wykorzystywany jako główny materiał płuczkowy w wierceń, szczególnie w technologii HDD. Jest to specjalna mieszanka bentonitu, która zapewnia stabilizację otworu wiertniczego.
Zastosowanie bentonitu w procesie wierceń niesie za sobą korzyści takie jak:
- bezproblemowy przebieg prac wiertniczych
- łatwy i szybki proces
- większa wytrzymałość masy formierskiej na ściskanie i zrywanie
- lepsza odporność na środowisko
Jednak zastosowanie bentonitu jako głównego składnika płuczki wiertniczej może generować potencjalne zagrożenia dla środowiska, zwłaszcza w przypadku technologii HDD.
Dodatki do bentonitu, takie jak siarczan baru i węglan wapnia, mogą wpływać na gęstość i skład chemiczny płuczki.
Inne materiały
Oprócz polimerów i bentonitu, w materiałach płuczkowych stosuje się również różne rodzaje inhibitorów korozji, takie jak:
- inhibitory korozji ogólnego działania
- inhibitory korozji kwasowej
- inhibitory korozji tlenowej
- inhibitory korozji mikrobiologicznej
Inhibitory te posiadają zaletę ochrony powierzchni metalu przed korozją, co odgrywa istotną rolę w procesie wiercenia.
Najczęściej wykorzystywane środki smarne w materiałach płuczkowych to oleje bazowe oraz różnorodne związki chemiczne, które zapewniają odpowiednie smarowanie narzędzi skrawających oraz skuteczne chłodzenie. Ich zastosowanie jest niezbędne do zwiększenia efektywności procesu wiercenia, poprawy jakości oraz wydajności pracy.
Dostosowanie materiałów płuczkowych do specyficznych potrzeb projektu
Dobór materiałów płuczkowych jest bardzo specyficzny dla każdego projektu wiercenia. Poprzez dokładną analizę warunków geologicznych oraz uwzględnienie wymagań technologicznych, dobór materiałów płuczkowych może mieć wpływ na efektywność prowadzenia wierceń. Wybór materiałów płuczkowych jest dokonywany w oparciu o analizę warunków geologicznych, co pozwala na kontrolę ciśnienia złożowego i efektywne wiercenie dzięki odpowiednio dobranym gęstościom płuczki.
Wybór materiałów płuczkowych jest również determinowany przez wymagania technologiczne, takie jak:
- odporność na naprężenia i zmęczenie
- właściwości chemiczne
- kompatybilność z innymi elementami przewodu wiertniczego
- warunki pracy wiercenia.
Analiza warunków geologicznych
Analiza warunków geologicznych przed wyborem płuczek polega na określeniu i ocenie warunków geologicznych gruntowych oraz analizie warunków geomorfologicznych w celu interpretacji właściwości gruntów i skał. Warunki geologiczne mogą mieć wpływ na skład i właściwości płuczek wiertniczych. Przykładowo, badania wykazały, że zastosowanie łupków mioceńskich jako płuczki może charakteryzować się dużymi właściwościami dyspersyjnymi i pęczniejącymi.
Dodatkowo, odpowiednie zastosowanie polimeru kapsułującego może poprawić właściwości smarne płuczek oraz wpłynąć na ich obniżenie i stabilizację.
Wymagania technologiczne
Ogólne technologiczne wymagania dla projektów wiertniczych obejmują wykonanie rurowania i uszczelniania rur okładzinowych zgodnie z zatwierdzonym projektem oraz wytyczenie otworu w terenie i zabezpieczenie terenu wiertni.
Wybór materiału płuczkowego ma bezpośredni wpływ na spełnienie wymagań technologicznych projektu wiertniczego, co umożliwia prawidłowe wykonanie prac oraz optymalizację procesu wiercenia.
Optymalizacja procesu wiercenia dzięki materiałom płuczkowym
Stosowanie odpowiednich materiałów płuczkowych ma kluczowe znaczenie dla optymalizacji procesu wiercenia. Poprzez zapewnienie stabilności ścian otworu, redukcję zużycia narzędzi wiertniczych oraz minimalizację problemów związanymi z utratą płuczek, materiały płuczkowe mogą znacznie poprawić efektywność i wydajność procesu wiercenia.
Materiały płuczkowe mogą wpływać na redukcję zużycia narzędzi wiertniczych poprzez zmniejszenie oporów hydraulicznych przepływu płuczki i momentu skręcającego przewodu wiertniczego.
Poprawa stabilności ścian otworu
Materiały płuczkowe, ze względu na swoje właściwości, takie jak zdolność do chwytania przewodu wiertniczego, tworzenia kawern i pęcznienia skał, wywierają istotny wpływ na stabilność ściany otworu wiertniczego. Ten wpływ jest uzależniony od odpowiedniej gęstości płuczki, która ma za zadanie utrzymanie stabilności.
Polimery i bentonity, dodawane do płuczki wiertniczej, odgrywają kluczową rolę w zachowaniu tej stabilności.
Redukcja zużycia narzędzi wiertniczych
Specjalistyczne płuczki wiertnicze, takie jak „Rotary Steerable System” (RSS), mogą zwiększać zużycie sprzętu i narzędzi wiertniczych, jednak odpowiednio dobrana płuczka może zmniejszyć to zużycie poprzez usprawnienie procesu wiercenia.
Cechy materiałów płuczkowych, takie jak zmniejszenie oporów hydraulicznych przepływu płuczki i momentu skręcającego przewodu wiertniczego, mają istotny wpływ na redukcję zużycia narzędzi wiertniczych.
Minimalizacja problemów związanych z utratą płuczek
Dobór właściwych materiałów płuczkowych może przyczynić się do minimalizacji problemów z utratą płuczek poprzez zastosowanie skutecznych środków do eliminacji zaników płuczek wiertniczych oraz zastosowanie technicznych rozwiązań, które zmniejszają zużycie płuczek i ograniczają utratę obiegu płuczek podczas procesu wiercenia.
Najbardziej efektywne materiały płuczkowe w minimalizacji utraty płuczek to specjalnie przygotowany bentonitowy środek do usuwania resztek płuczki oraz preparat płuczkowy Stuewa Clean.
Bezpieczeństwo i ekologia w użytkowaniu materiałów płuczkowych
Podczas wyboru materiałów płuczkowych, oprócz ich skuteczności i efektywności dla procesu wiercenia, istotne jest również ich bezpieczeństwo oraz wpływ na środowisko.
Niektóre materiały płuczkowe są szczególnie bezpieczne dla środowiska i ulegają biodegradacji po zakończeniu procesu wiercenia, co jest istotne dla ochrony środowiska.
Biodegradowalność
Materiały płuczkowe, takie jak bentonit i polimery, wykazują właściwości biodegradowalne. Biodegradowalność oznacza ich zdolność do rozkładu przez mikroorganizmy po zakończeniu procesu wiercenia, co jest istotne dla ochrony środowiska.
Zarządzanie odpadami wiertniczymi
Należy pamiętać, że proces wiercenia generuje odpady, które muszą być odpowiednio zarządzane, aby minimalizować ich wpływ na środowisko. W Polsce obowiązują krajowe regulacje prawne dotyczące odpadów wiertniczych. Kwestie odpadów wydobywczych reguluje ustawa o odpadach z dnia 10 lipca 2008 r.
Ponadto istnieje rozporządzenie Ministra Klimatu i Środowiska z dnia 10 maja 2021 r. dotyczące sposobu selektywnego zbierania wybranych frakcji odpadów.
Podsumowanie
Materiały płuczkowe są kluczowe dla efektywnego i efektywnego wiercenia. Wybór odpowiednich materiałów płuczkowych, które są dostosowane do specyficznych warunków geologicznych i technologicznych, może przyczynić się do optymalizacji procesu wiercenia. Ponadto, odpowiednie zarządzanie odpadami wiertniczymi i wybór materiałów, które są bezpieczne dla środowiska, są istotne dla zrównoważonego procesu wiercenia.
Najczęściej zadawane pytania
Ile bentonitu do płuczki?
Do płuczki bentonitowej zaleca się dodanie 1,5-2,0 kg/m3, natomiast jako samodzielna płuczka dodaje się 2,0-3,0 kg/m3. Warto pamiętać, żeby mieszać powoli, aby zapobiec zbryleniu.
Jaką płuczka do wiercenia studni?
Najlepszą płuczką wiertniczą do studni jest płuczka bentonitowa ze względu na jej silne właściwości absorpcyjne.
Na czym polega przewiert sterowany?
Przewiert sterowany polega na bezwykopowym wykonywaniu instalacji pod terenowymi elementami infrastruktury, przy użyciu odpowiednich maszyn wiertniczych. Jest to przydatne rozwiązanie do zastosowania w różnych rodzajach gruntu.
Ile kosztuje przewiert sterowany?
Przewierty sterowane kosztują około: fi 40 – 63 mm: 50-70,00 zł, fi 90-110 mm: 75-90,00 zł, fi 125 mm: 90-110,00 zł.
Ile kosztuje maszyna do przewiertów sterowanych?
Maszyna do przewiertów sterowanych kosztuje 280 000 euro netto. Możesz uzyskać więcej informacji pod numerem telefonu +48 664 410.
Tekst promocyjny